Flanges
Caman Engineering offers quality flanges that meet Australian & Global standards. Our range includes weld neck flanges, slip-on flanges, blind flanges, and custom items, available in various sizes and materials.
Size Range and Specifications
Size Range |
15mm-1500mm (1/2"-60") |
---|---|
Flange Standard |
ASME/ANSI B16.5, ASME/ANSI B16.47, EN1092, AS2129, AS/NZ 4087, API Spec 6A. |
Sealing Type |
Flat Face, Raised Face, Ring Joint |
Sealing Finish |
Spiral Finish 3.2 µm-12.0 µm |
Flange Materials |
A105, A350LF2, LF3, LF6, A694 F42-F70, AS/NZS3678 Gr250, 304, 316, 2205 (A182 F51), 2207, Incoloy 625 or as requested. |
Delivery |
Standard: Same-day Delivery, many sizes ex stock.Custom: 5-10 days |
Varieties |
Our range includes Weld Neck flanges, Blind flanges, Slip-on flanges, Socket Weld flanges, Lapped flanges, and Long Weld Neck flanges. |
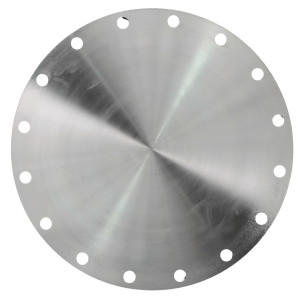
Custom Manufacturing - Flanges
Our ISO 9001 certified facility handles specialized requirements including:
- Custom material selection for Weld Neck, Slip-on, and Blind flanges
- Specialized construction methods and fabrication
- Complete material traceability with ITP/MDR documentation
- Project-specific packaging and specifications
- 10-20 days for custom items, many sizes in stock.
As an ISO 9001 certified manufacturer, we accommodate specialized engineering requirements through custom material selection and proven construction methods. Our comprehensive quality system includes full material traceability, detailed testing documentation, and certification packages. We provide complete documentation including ITPs and MDRs. All products can be packaged according to your specific engineering or project requirements, delivered within rapid timeframes.
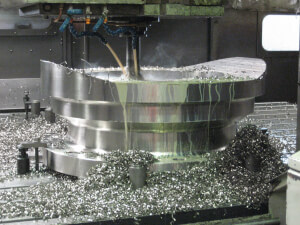
What are Flanges?
Flange is a generic description used to describe a device that terminates a pipe or device and provides a boltable joint. The concept is generic but the application is specific. Flanges are pre-designed to meet process conditions. Standards exist that provide standardised dimensions and material types.
Flange Types
Weld Neck Flanges
Weld Neck flanges are designed with a long tapered hub that gradually transitions from the flange thickness to the pipe wall thickness. This design provides:
- Superior reinforcement for high-pressure applications
- Excellent resistance to bending and thermal cycling
- Full penetration weld joint
- Ideal for extreme temperature and pressure conditions
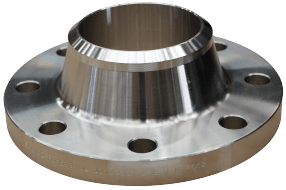
Slip-on Flanges
Slip-on flanges slide over the pipe and are welded both internally and externally. Features include:
- Lower cost alternative to weld neck flanges
- Easier alignment during installation
- Suitable for lower pressure applications
- Common in general industrial applications
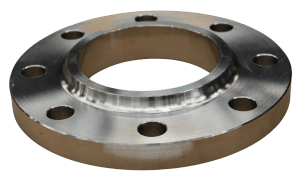
Blind Flanges
Blind flanges are solid disk-shaped flanges used to:
- Terminate or seal the end of piping systems
- Provide access for cleaning or inspection
- Allow for future system expansion
- Create temporary closures in piping systems
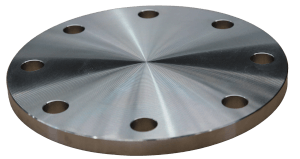
Socket Weld Flanges
Socket weld flanges feature a socket cavity that accepts the pipe. Ideal for:
- Small diameter high-pressure piping
- Nuclear and other critical applications
- Systems requiring frequent dismantling
Threaded Flanges
Threaded flanges have internal threads that mate with pipe threads. Best suited for:
- Applications where welding is not permitted
- Temporary connections
- Low-pressure systems
Lap Joint Flanges
Lap joint flanges work in conjunction with stub ends and offer:
- Easy rotation for bolt hole alignment
- Cost-effective solution for exotic materials
- Simplified maintenance and replacement
Flange Tables and Standards
AS2129 | Australian Standard |
Flanges for piping valves & fittingsA common industrial flange in Australia. Sold mostly with a spiral finish on a flat face. Used for water movement and general industrial fluids, including in the food and wine industry. |
AS4087 | Australian and New Zealand Standard |
Metallic flanges for waterworks purposesUsed generally for water supply projects such as government sponsored projects. Similar hole spacings to some AS2129 flanges. |
ASME B16.5 | American Society of Mechanical Engineers |
Pipe flanges & flanged fittingsThis is the mainstay for most heavy industrial and petrochemical plants. Covers flanges up to 600mm typically supplied with a raised face and spiral finish. |
ASME B16.47 | American Society of Mechanical Engineers |
Large diameter steel flangesFound mostly in heavy industrial and petrochemical applications. Covers flanges above 600mm typically supplied with a raised face and spiral finish. Available in A and B type. |
BSEN 1092-1 | British Industrial Flanges |
Flanges & their jointsFound on DIN pumps and other equipment from Europe and the UK.NB similar BS4504. |
JIS B2220 | Japanese Industrial Standard |
Steel pipe flangesThese are seen mostly in Australia in ships. |
ASME B16.36 | American National Standard |
Orifice FlangesThese flanges are designed to sit either side of orifice plates for measuring flow. They will typically be supplied with a side port and jacking bolts. |
ASME B16.48 | American National Standard |
Line BlanksSpectacle Blinds, Fig 8 Blinds, Spades, Paddle Blinds, Spacers. |
MSS SP-44 | American Manufacturing Standardisation Society |
Steel Pipeline FlangesSimilar ASME B16.47A. |
AWWA C207 | American Water Works Association |
Steel Pipe Flanges for WaterworksSome flanges have similar hole spacing to ASME B16.47A. |
API 605 | American Petroleum Institute |
Large Diameter Carbon Steel FlangesSimilar ASME B16.47B. |
Sealing Face Finishes - Flanges
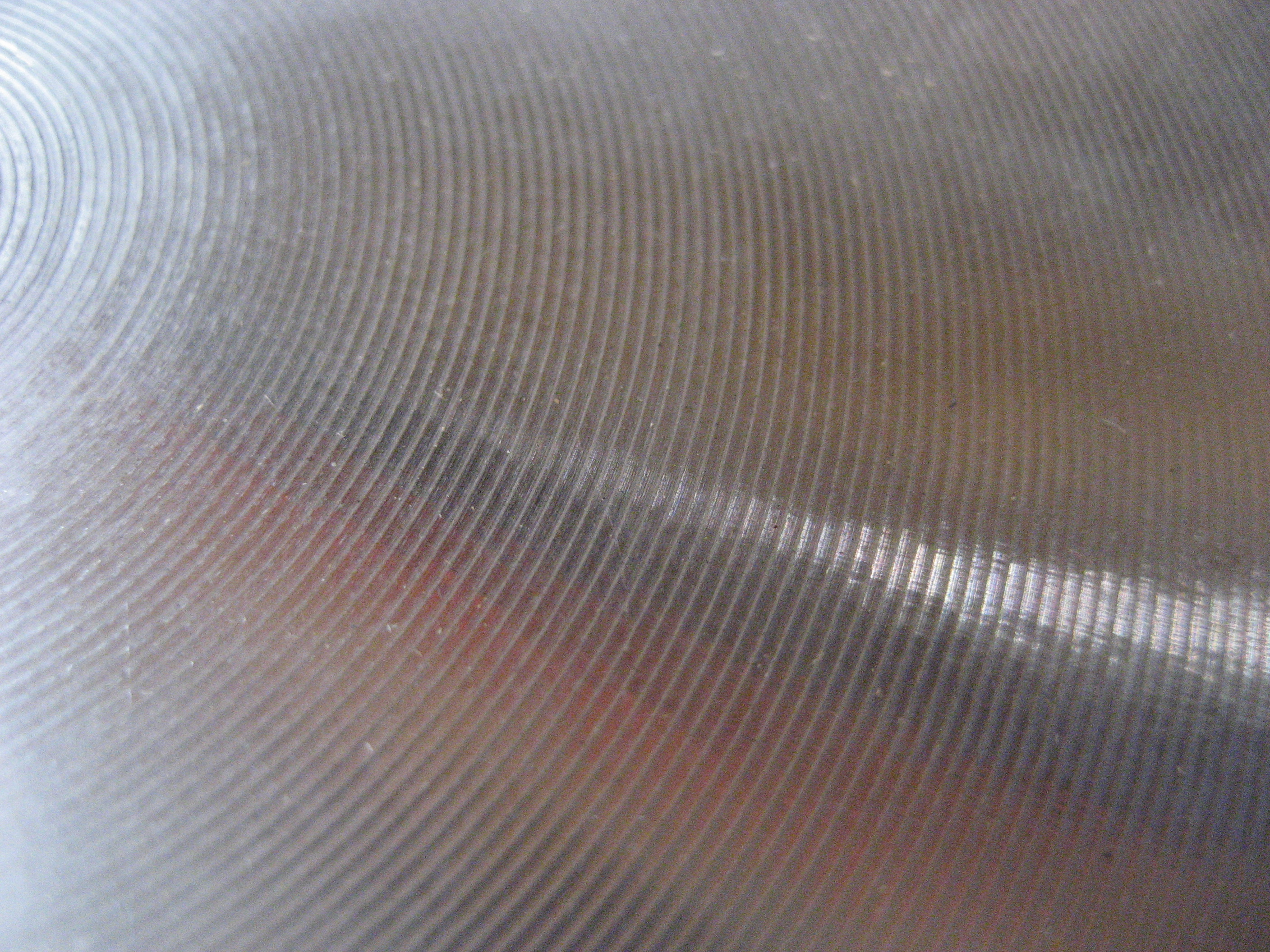
Flange Spiral Sealing Faces
Typically Weld Necks, Slip-ons and Blinds are produced as a raised face, flat face, or ring joint sealing surface depending on the application requirement. The spiral sealing face is a specified finish typically Ra 3.2um-6.3um.
Australian and New Zealand flange standards specify coarser sealing faces which are typically Ra 6.4um-12um.
Material Selection & Surface Treatments - Flanges
As an ISO 9001 certified Australian manufacturer, we produce flanges using materials that meet specific client testing requirements. Our comprehensive range includes:
Material Options
- Carbon Steels: Carbon Steel (AS1548 460NR, A516 Gr70), Forged Carbon Steel (A105, A350 LF2, A350 LF3)
- Stainless Steels: Stainless Steel 316L (A240 P316L, A182 F316L), Stainless Steel 304L (A240 P304L, A182 F304L), Duplex Steel (UNS31803), Super Duplex (2207), Incoloy (625)
Surface Treatment Options
We offer specialized surface finishes including:
- Industrial galvanizing
- PTFE coatings and linings
- Various epoxy finishes
Corrosion Protection and Packaging - Flanges
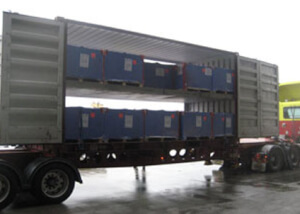
Weather-protected shipment
Each flange will always have a sealing face that requires protection. Weld Necks have an additional weld preparation that also requires protection. Whether you want the flanges preserved for 2 weeks or 2 years, Caman Engineering have packing system that ensures that your Weld Neck, Slip-on and Blinds arrive at the installation in good condition. Even more robust corrosion protection can be supplied upon request.
Manufacturing & Quality Assurance
Product Identification
Each flange is permanently marked with identification details including:
- Material grade
- Heat number
- Relevant standards
- Production traceability
Quality Testing
Comprehensive quality testing ensures:
- Compliance with specifications
- Meeting industry standards
- Dimensional accuracy
- Material verification
Corrosion Protection
Special attention is given to protecting:
- Sealing faces
- Weld preparations
- Critical surfaces
- Machined areas
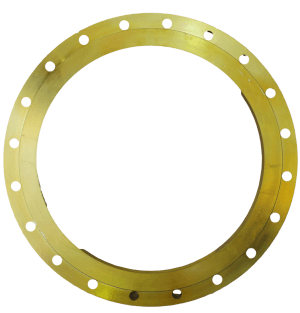
Secure Packaging
Our packaging process ensures:
- Protection during transport
- Timely arrival
- Safe handling
- Product integrity
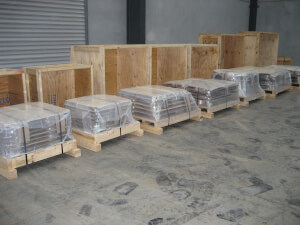
FAQ About Industrial Flanges
Weld neck flanges feature a long tapered hub that gradually transitions to the pipe wall thickness, providing superior reinforcement for high-pressure applications. They require a full penetration weld and are ideal for extreme temperature and pressure conditions.
Slip-on flanges, on the other hand, slide over the pipe and are welded both internally and externally. They are a lower-cost alternative, easier to align during installation, but are generally suitable for lower pressure applications.
Selecting the right flange standard depends on several factors:
- Industry requirements: Different industries follow different standards (e.g., ASME for petrochemical, AS2129 for Australian water industry)
- Pressure rating: Higher pressure applications require appropriate pressure class flanges
- Temperature conditions: Extreme temperatures may require specific materials and designs
- Regional regulations: Local codes may mandate specific standards
Consult our flange standards reference guide or contact our engineering team for assistance with your specific application.
For corrosive environments, we recommend:
- Stainless Steel 316/316L: Excellent resistance to most chemicals and saltwater environments
- Duplex (2205) and Super Duplex (2507): Superior corrosion resistance with higher strength than standard stainless steels
- Incoloy 625: Exceptional resistance to extreme corrosive conditions, particularly in high-temperature environments
The specific material selection should be based on the particular corrosive agents present, temperature, and pressure conditions. Our engineering team can provide guidance for your specific application.
The flange face finish is critical for creating an effective seal between mating flanges. The surface roughness (measured in Ra or RMS) affects how well the gasket conforms to the flange surface.
Different applications require different finishes:
- Spiral serrated (3.2-6.3 μm): Most common for raised face flanges in industrial applications
- Smooth finish (1.6-3.2 μm): Used with soft gaskets or for high-pressure applications
- Rough finish (6.4-12.5 μm): Common in Australian standards for water applications
The correct finish ensures proper gasket compression and prevents leakage under operating conditions.
Need Standard or Custom Flanges?
Contact our knowledgeable team today to discuss your Flanges requirements.
Get A Quote